Magnetfinish – Precision Edge Honing & Polishing for Cutting Tools
Magnetfinish is a remarkable and unique process that was originally developed to dramatically increase the performance and lifetime of all types of cutting tools. Generally, cutting tools that have been Magnetfinished can last over twice as long and be run at much higher speeds and feeds.
How It Works
Magnetfinish uses magnetically guided abrasive powder to polish cutting tools to a surface roughness as low as 0.02 μm Ra. It precisely rounds tip and flute edges to between 3–50 μm, improving consistency and tool geometry. This process enhances chip flow, extends tool life by removing the run-in phase, and improves coating adhesion by preparing surfaces prior to coating.
Applications
Ideal for taps, drills, end mills, reamers, and stamping tools, Magnetfinish is also used on automotive components and precision parts. It delivers burr-free finishes and consistent edge rounding on both coated and uncoated tools, boosting performance and durability.
.png)
Magnetfinish MF66
Precision Surface Finishing with Enhanced Efficiency
The MF66 offers leading-edge surface quality, productivity, and an excellent price-performance ratio.
Key Features:
-
Wear-Free Robotic Movements: All tool movements are executed by a maintenance-free robot, ensuring consistent performance.
-
Expanded Tool Storage: Accommodates up to 120 tools, doubling previous capacities for increased efficiency.
-
Controlled K-Factor Processing: Allows precise control over both the tool tip and cylindrical parts for tailored finishing.
-
Reduced Process Times: Optimised for faster honing of drills, ball-end mills, and similar tools.
-
Dual-Process Capability: Performs cylinder honing and flute polishing in a single run with separately adjustable process times.
-
Enhanced HMI: Features an onboard 17" screen for improved user interaction and control.
.png?width=1280&height=720&name=Your%20paragraph%20text%20(68).png)
Magnetfinish MF76
Advanced Automation for High-Volume Production
The MF76 represents a completely new design, building upon 15 years of Magnetfinish machine development. It sets the standard for surface quality, productivity, and automation.
Outstanding Properties:
-
Versatile Pallet Compatibility: Supports all standard pallet types, such as Rollomatic, and offers customisation options.
-
Dual-Robot System: Utilises two robots operating in parallel to achieve the shortest possible cycle times.
-
User-Friendly Operation: No specialised robot knowledge required, thanks to online offset correction capabilities.
-
Tool Tracking Functionality: Incorporates a tool track function for enhanced process monitoring.
-
Extended Unattended Operation: Designed for very long man-less runs, maximising productivity.
Before
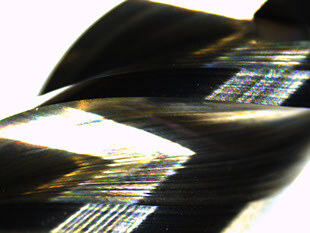
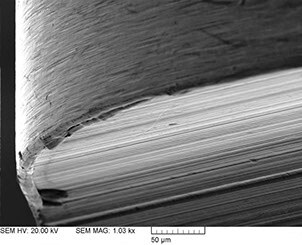
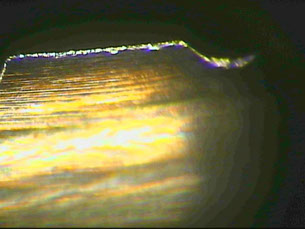
After
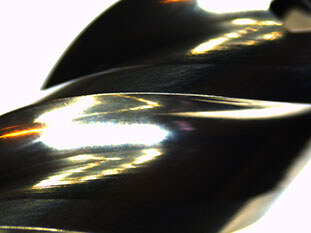
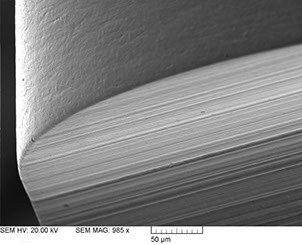
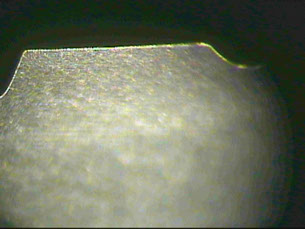
Why Choose Magnetfinish?
Leading Surface Solutions
-
Ultra-Fine Surface Finish
Achieves surface roughness as low as Ra = 0.02 µm, enhancing component performance. -
Precise Edge Rounding
Consistently produces edge radii between 3 and 50 µm, improving tool durability and cutting efficiency. -
Material Versatility
Effective on magnetic materials like HSS, lightly magnetic materials such as carbide, and non-magnetic materials including cermet.
-
Enhanced Tool Performance
Polishing flutes improves chip flow, while edge honing extends tool life and performance. -
Coating Preparation
Prepares tools for coating by removing droplets and polishing the surface, resulting in better coating adhesion and reduced friction. -
Reproducibility
Delivers consistent, repeatable results, making it suitable for high-volume production environments.
Magnetfinish: Advanced Finishing and Automation Technologies
Visit Magnetfinish's Website for The Latest Developments in Surface Finishing Solutions